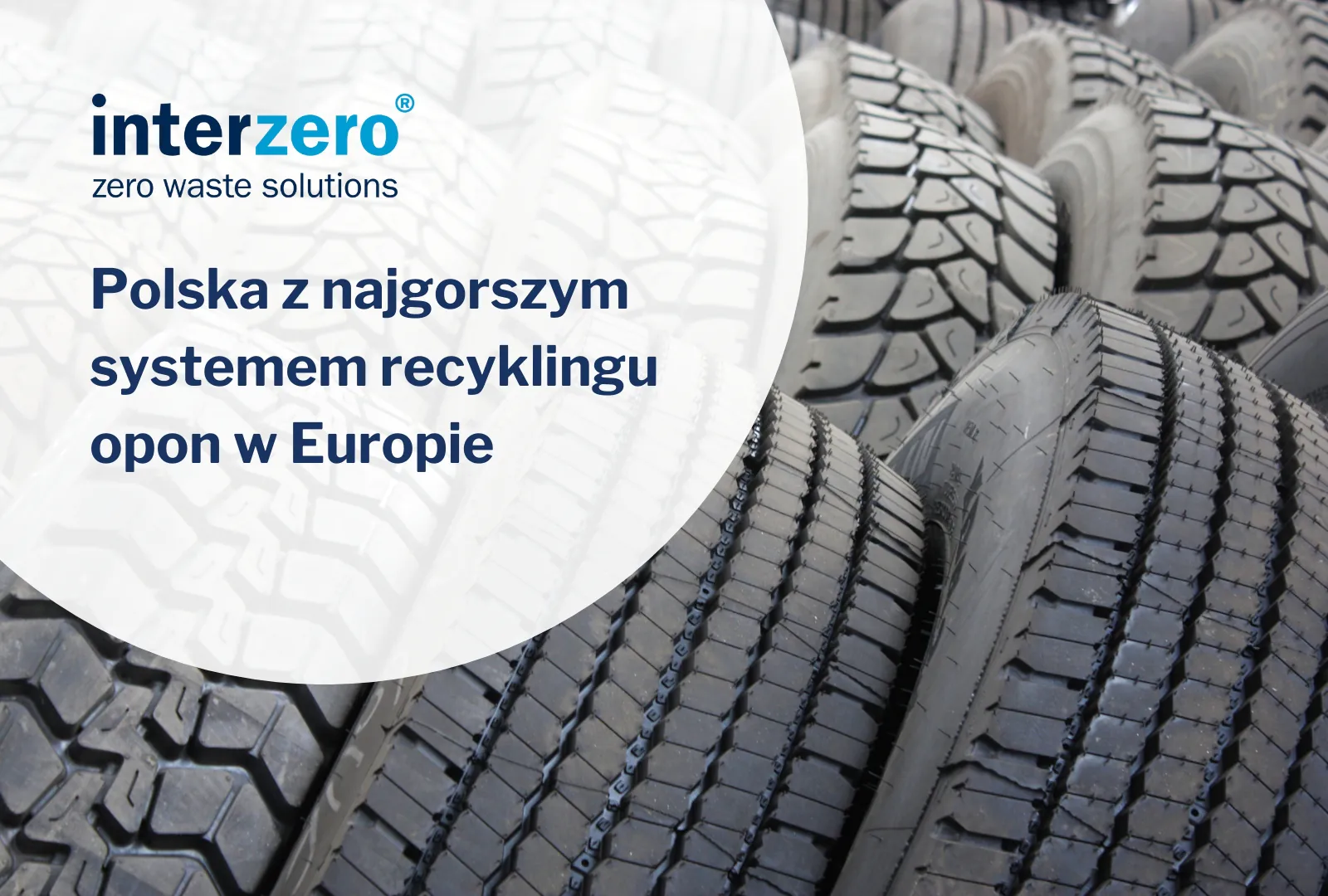
Poland with the worst tyre recycling system in Europe
Every year in Poland, as many as 25 000 waste tyres end up in wild landfills. Only 75% of pneumatic tyres are handed over to processing plants, and solid tyres are not recycled at all. At the same time, the industry has long struggled unsuccessfully to bring Polish tyre recovery regulations into line with EU regulations. These and many more problems of the tyre recycling industry are highlighted in a report by the Polish Tyre Recycling Association.
The 10 deadly sins of Polish tyre recycling
Poland's tyre ROP has not worked for many years, recovery levels are not in line with EU regulations and the whole tyre recycling system in our country is dysfunctional - these are the conclusions of the report A story that goes round and round developed by the Polish Tyre Recycling Association (PSRO). At the beginning of the publication, the authors list 10 facts that show the scale of the problem.
Among all EU Member States Poland is in the infamous 1st place in terms of the number of unused tyres - we are responsible for 60% of the mass of all untreated tyres throughout the Community! We also have lowest effective recycling rate, the second least demanding ROP regulations on tyres and the second lowest real environmental charges. Consequently:
- Every 4th pneumatic tyre and all solid tyres are not recycled or recovered,
- 1 in 1,000 tyres sold is discarded into the environment,
- Every 4th pneumatic tyre is incinerated in the furnaces of cement works. Every year, around 50,000 tyres go into these furnaces!
Meanwhile, domestic tyre recycling facilities can process 100% of tyres placed on the market. Each year, we buy between 280,000 tonnes and 350,000 tonnes of tyres, while the total capacity of processing plants is over 400,000 tonnes. As PSRO reports:
250 km - this is how many new motorways and motorways each year MAY be made safer, more durable and quieter by using recycled tyre products in their construction
What does the Polish ROP system look like on tyres?
The ROP system for tyres was introduced by the Act of 11 May 2001 on the obligations of entrepreneurs with regard to the management of certain waste and the product fee. It obliged manufacturers and importers to the achievement of the annual targets for recovery and recycling of tyres - they currently amount to:
- 75% for recovery,
- 15% for recycling.
Failure to comply with these obligations means that a product charge of PLN 2.20 per kg of tyres. Find out the most important information about the product levy on cars and tyres for the autocommerce >>.
Each manufacturer and importer is free to choose whether it wants to fulfil the obligations as an introducer on its own or whether it prefers to entrust these to a recovery organisation. Interzero takes over all the duties of tyre introducers, including those of car dealers and other traders. Find out why you should hand over your tyre recovery and recycling duty to Interzero!
Tyre collection and recycling system to be improved - what should the new tyre ROP be?
The PSRO report indicates that the Polish ROP and tyre recycling system not implements the polluter-pays principle", and it is not the responsibility of manufacturers and importers, but of municipalities (including PSZOKs) and tyre recyclers carrying out collections. It is necessary to reverse this mechanism and shift the responsibility to those introducing the. According to the PSRO, this will require, among other things:
- Increase annual levels of recycling (to 50%) and recovery (to 100%) of tyres.
- To also cover solid tyres, which are currently excluded from the ROP, under the extended manufacturer's liability scheme.
- Sealing the tyre recovery and recycling system.
- Adhering to the statutory waste hierarchy - promoting recycling before incineration.
In addition, the authors of the report draw attention to the need for implementation into Polish law of the provisions of the Waste Directive (2008/98/EC) and the Directive amending the Waste Directive (2018/851/EU), which would aim to give priority to recycling over other forms of recovery and to prevent the incineration of separately collected waste (including tyres).
What does tyre recycling look like?
Mechanical recycling (also known as raw material recycling) of waste tyres is the most environmentally beneficial way of managing them. It consists of a multi-stage grind (cutting, crushing, grinding), resulting in rubber pellets.
As the authors of the report point out, submitting tyres for mechanical recycling reduces their carbon footprint by 4 to 5 times compared to incineration. It also significantly reduces water consumption and environmental impact by 76-80%.
How do I send my tyres for recycling? Book a professional waste tyre collection at Interzero! Fill in the short form and get the best offer for tyre disposal >>
What is produced from tyre recycling?
The mechanical recycling process of waste tyres does not only recover rubber granules, but also steel wire and textile cord. The pellets are used, among other things, for the manufacture of:
- bituminous surfaces, e.g. for playgrounds, running tracks and playing fields,
- anti-vibration pads,
- industrial carpets,
- road surfaces (as a component of asphalt).
The recovered steel is remelted and returned to circulation. Textile cord is currently used as an alternative fuel; however, work is underway to use it in thermal insulation materials and in construction and road building.
Used tyres can also be retreadedwhich will make them reusable without having to process them in their entirety. Old tyres are also used to build retention walls in civil engineering (e.g. as barriers on race tracks) and water engineering (e.g. as bumpers).
Sources:
- Polish Tyre Recyclers Association, A story that goes round and round. A report on the long-standing dysfunctions of the tyre recycling system in Poland, including how 25 000 tyres a year end up in wild landfills, https://psro.eu/wp-content/uploads/2024/10/Raport-PSRO-2024.pdf